Combined corrosion and fatigue strength of joined materials for body-in-white and structural automotive applications design
AutoFatCor (RFSR-CT-2011-00021)
—
Start: 01/09/2011
Duration: 42 months
Coordinator: French Corrosion Institute
Participants: ArcelorMittal Maizières Research, Voestalpine, BMW, CSM and GSI
Budget: 1 768 888 €
EU contribution: 1 061 333 €
—
For the first time, automotive assemblies have been studied in AutoFatCor project under simultaneous corrosion-fatigue loading in cyclic corrosion tests designed to mimic closely service exposure conditions. The aims of the project were to provide new tools [1], including the combined corrosion-fatigue solicitations for the design of automotive components involving assembly made both of traditional and new steel based materials to achieve efficient lightweighting. The industrial aim was to obtain a useful method to predict fatigue life of automotive components under atmospheric weathering conditions.
Steel panels were assembled by conventional resistance spot welding, adhesive bonding and combination of the two processes in both lap-shear and T-peel designs. Panels were exposed on a vehicle, at a field station and in various accelerated corrosion tests.
Fatigue-corrosion tests were performed following two procedures, alternated and simultaneous modes. Additional simultaneous fatigue-corrosion tests were also performed on a restricted number of configurations for 4 different climatic conditions to study the influence of climatic parameters [2–4].
Spot-welded lap-shear specimens were not sensitive to alternated fatigue-corrosion, whereas a decrease of the fatigue life at high load amplitude and an increase at lower load levels was observed in simultaneous fatigue-corrosion conditions. For adhesive bonded specimens, a large effect of the corrosive environment was reported, even higher for the simultaneous fatigue-corrosion tests than for alternated fatigue-corrosion conditions. No beneficial effect from adhesive and spot weld bonded specimens was noticed in comparison with only adhesive bonded specimens.
Specimens were more affected by twelve weeks in accelerated corrosion test than almost two years of outdoor exposure.
Modeling based on notch stress approach was successfully developed for spot weld specimens. For adhesive specimens, the cohesive zone model required further development to accurately predict the life duration during fatigue-corrosion.
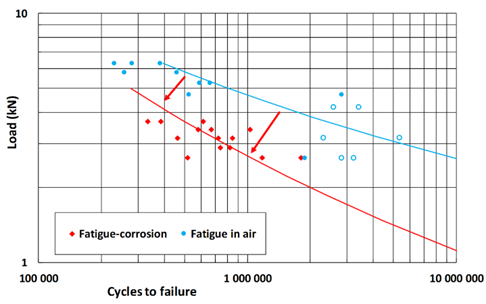
Figure 1: Example of SN curves under fatigue and fatigue-corrosion conditions and fatigue test benches in corrosion cabinet.
References:
[1] N. LeBozec, D. Thierry, A new device for simultaneous corrosion fatigue testing of joined materials in accelerated corrosion tests, Mater. Corros. 66 (2015) 893–898. https://doi.org/10.1002/maco.201407984.
[2] D. Thierry, F. Vucko, G. Luckeneder, B. Weber, L. Dosdat, T. Bschorr, K. Rother, Fatigue behavior of spot-welded joints in air and under corrosive environments – Part II, Weld. World 60 (2016) 1231–1245. https://doi.org/10.1007/s40194-016-0367-z.
[3] D. Thierry, F. Vucko, G. Luckeneder, B. Weber, L. Dosdat, T. Bschorr, K. Rother, Fatigue behavior of spot-welded joints in air and under corrosive environments – Part I, Weld. World 60 (2016) 1211–1229. https://doi.org/10.1007/s40194-016-0366-0.
[4] F. Vucko, N. LeBozec, D. Thierry, B. Weber, L. Dosdat, G. Luckeneder, T. Bschorr, K. Rother, C. Sciaboni, J. Sczepanski, Combined corrosion and fatigue performance of joined materials for automotive applications, Mater. Corros. 67 (2016) 1143–1151. https://doi.org/10.1002/maco.201608962.
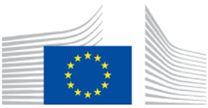
Funding of the project by the European Commission, Research Program of the Research Fund for Coal and Steel, Technical Group: TGS7 Steel products and applications for automobiles, packaging and home appliances under the Grant Agreement No RFSR-CT-2011-00021